LDAR Inspections | Best Practices for LDAR Compliance
On May 7, 2024, the U.S. Environmental Protection Agency (EPA) issued its final version of updates to 40 CFR Part 60 for New Source Performance Standards (NSPS) for Crude Oil and Natural Gas Facilities, including subparts OOOOb and Emissions Guidelines EG OOOOc, which we call OOOOb_c, collectively. Together with other changes to federal regulations, the agency’s stated objective is to reduce further emissions from the Oil and Gas sector.
One of the focus areas of regulation is the reduction of fugitive emissions from oil and gas production operations.
The "Quads" and Compliance for Oil and Gas Facilities
Given that NSPS OOOOb_c are just the latest updates in a string of rule making, it can be confusing as to which Subpart, or standard, applies to what facilities. The table below sorts out which rule applies, depending on the date a facility was placed into service.
Subpart | Source type | Applicable dates |
40 CFR part 60, subpart OOOO | New, modified, or reconstructed sources | After 08/23/2011, and on or before 09/18/2015 |
40 CFR part 60, subpart OOOOa | New, modified, or reconstructed sources | After 09/18/2015, and on or before 12/06/2022 |
40 CFR part 60, subpart OOOOb | New, modified, or reconstructed sources | After 12/06/2022 |
40 CFR part 60, subpart OOOOc | Existing sources | On or before 12/06/2022 |
Source: Page 16828 Federal Register/Vol. 89, No. 47/Friday, March 8, 2024/Rules and Regulations.
Facilities affected by OOOOb_c must be in compliance with the regulations by May 7, 2024, or upon initial startup, whichever occurs later.
This article covers the key aspects of LDAR best practices necessary for compliance and should not be considered a comprehensive summary or guide of the rules. We encourage you to reach out to a qualified resource to evaluate your specific operations.
What Oil and Gas Facilities are Subject to OOOOb?
The types of oil and gas production facilities covered under NSPS OOOOb and EG OOOOc standards are comprehensive and include e a wide range of sites using components that can generate fugitive emissions, including:
Fugitive Emissions Components Affected Facilities. Any facility that uses fugitive emissions components.
Well Affected Facilities. Well sites, including single wells drilled for oil or natural gas production.
Compressor Affected Facilities. Any facility using single centrifugal or reciprocating compressors.
Process Controller Affected Facilities. Operations using natural gas-driven process controllers.
Storage Vessel Affected Facilities. Includes tank farms (batteries) with specified emissions potential. Think tank farm at a centralized storage facility or on a multi-well pad.
Process Unit Equipment Affected Facilities. Essentially all equipment within a process unit at an onshore natural gas processing plant.
Sweetening Unit Affected Facilities. Facilities with units that process natural gas and recover sulfur (e.g., Amine units).
Pump Affected Facilities. Operations that use natural gas-driven pumps.
Monitoring Requirements for Fugitive Emissions Components
In this blog, we focus on Fugitive Emissions Components Facilities, simply because the definition is so broad as a practical matter it conceivably covers nearly every oil and gas production facility.
The table below summarizes the emissions monitoring requirements for Fugitive Emissions Components Affected Facilities, based on their type.
Type | Frequency | Type |
Fugitive emissions component affected facilities located at single wellhead only well sites | At least quarterly* | AVO, or any other detection method, after the initial survey (see Note below for exceptions) |
fugitive emissions component affected facilities located at small well sites | At least quarterly* | AVO, or any other detection method, after the initial survey (see Note below for exceptions)
and include a visual inspection of all thief hatches and other openings on the storage vessel that are fugitive emissions components must be conducted in conjunction with the monitoring survey to ensure that they are kept closed and sealed at all times except during times of adding or removing material, inspecting or sampling material, or during required maintenance operations.
At small well sites with a separator, a visual inspection of all separator dump valves to ensure the dump valve is free of debris and not stuck in an open position must be conducted in conjunction with the monitoring survey |
fugitive emissions components affected facilities located at multi-wellhead only well sites | A monitoring survey must be conducted at least quarterly* | AVO at least quarterly (see Note below for exceptions)
OGI at least semiannually or Method 21 after the initial survey. Consecutive semiannual surveys must be conducted at least 4 months apart and no more than 7 months apart. |
fugitive emissions components affected facilities located at well sites or centralized production facilities that contain the major production and processing equipment | At least quarterly* | OGI or Method 21. Consecutive quarterly monitoring surveys must be conducted at least 60 calendar days apart. (see Note below for exceptions)
|
Source: Page 16871 Federal Register/Vol. 89, No. 47/Friday, March 8, 2024/Rules and Regulations.
Of course, there are always exceptions to every rule and NSPS OOOOb_c is no exception. It is important to note that if a Fugitive Emissions Components Affected Facility contains any of the following equipment, it is subject to a minimum of bimonthly inspections using AVO, or other detection method, after the initial survey, to include all thief hatches and separator dump valves:
One or more controlled storage vessels or tank batteries.
One or more control devices.
One or more natural gas-driven process controllers or pumps.
Two or more pieces of major production and processing equipment not specified above.
READ MORE: AVO Inspections
READ MORE: Leak Detection and Repair Services
Fugitive Emissions Repair Requirements
If fugitive emissions are detected, the repairs must be initiated within these timelines:
For emissions detected using AVO, repairs must begin within 15 calendar days of detection, and completed within another 15 days.
For emissions detected via OGI or Method 21, repairs must begin within 30 days, and completed within another 30 days.
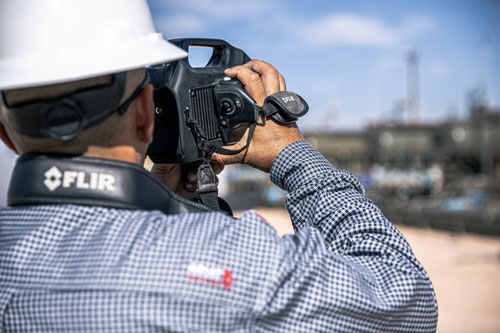
LDAR Best Practices (The Platinum Control Advantage)
Compliance with emissions monitoring standards in OOOOb_c is critical to maintaining uptime, minimizing the risk of fines, which can be significant, and keeping more natural gas product in the pipe for sale. Implementing LDAR best practices not only ensures compliance but also enhances operational efficiency and reduces environmental impact.
Platinum Control has developed best practices for LDAR inspections to maximize the efficiency of our LDAR teams and ensure our customers maintain compliance at a competitive cost.
The Best Practices for LDAR inspections include:
Coordination and Collaboration. Our teams work in partnership with yours, ensuring seamless integration and timely communication. We consider ourselves professionals and act like members of your team.
Dual Crews for Immediate Response. We typically run our inspection and repair teams together simultaneously. Upon detection of emissions during inspections, the repair crew can fix leaks in real time while the inspection team is on-site. This ensures leaks are fixed promptly, minimizing the potential for further emissions and environmental impact.
Quality Instruments and OGI. We use high quality equipment, including OGI cameras, to detect and verify repairs swiftly, reducing the likelihood of oversight and the need for rework. We maintain our equipment rigorously to ensure it is calibrated regularly for accurate readings.
Record Keeping. We generate and deliver comprehensive, quality reports to evidence compliance and verify repairs.
Our objective is to help you exceed compliance. Rather than just meeting regulatory requirements, we strive to help customers exceed them. By setting internal standards that surpass minimum regulatory thresholds, facilities can enhance environmental stewardship and build a reputation for proactive compliance.
Summary
Adhering to LDAR best practices makes compliance with NSPS OOOOb and EG OOOOc efficient and effective. Our best practice of sending inspection and repair crews to the site at the same time significantly reduces the potential for rework or even missing a requirement. Fixing leaks fast and reliably not only ensure compliance but also contributes positively to environmental sustainability efforts.
Contact us today to learn more about how LDAR services from Platinum Control can help you ensure compliance and maximize operational efficiency.
Contact:
Chance Lauer
VP Sales & Service
Platinum Control
Email: clauer@platinumcontrol.com
Phone: 800-994-0579
About Platinum Control
Our core competency in Facilities Optimization sets us apart. We work with operators in the Permian Basin of all sizes, from companies having only a handful of wells to supermajors. As a result, we leverage the experience gained with larger operators, build best practices into our products and services, and then disseminate that knowledge to our smaller customers.
A well site or facility with an optimized configuration will help you harness its full potential, maximizing its long-term economic value and environmental performance.
Comments